A lack of resources encourages innovative thinking!
Leading players in the industry, has introduced groundbreaking solutions that not only enhance production capabilities but also minimize environmental impact.
Digitalization and big data are transforming the aftermarket, enabling efficient testing, precise virtual assistance, and streamlined documentation.
Contact me
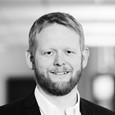
How does this effect the insulation equipment aftermarket?
In the current market, everybody is afraid to be short in supply and unable to deliver what has been promised. So, the customers are very keen on aftermarket solutions that enable them to produce more with less. Innovative solutions and smarter ways of doing things have always been in demand. Now, I think it is fair to say, that there is a higher demand – and a keener ear – in the market for solutions that can impact both production and footprint in a positive way.
Is it new add-ons to existing machinery that are the key selling points for Qubiqa?
Some of it is down to that, yes. For instance, Qubiqa has a patented welderbar called FlexWeld, which is doing quite well now. It is a smarter way to weld packaging that enables our clients to reduce the amount of plastic needed by almost 50%.
Normally, this would be a good business case, but now it is an outstanding one. In a world in which there is a shortage of supply, raw material prices are skyrocketing, and with increased taxes on films, there is an even higher push towards sustainable production.
Do shortages drive innovation?
In a way, yes. A lack of resources encourages innovative thinking! MDO film is a good illustration of this. It was developed to reduce plastic use and made it possible to use either thinner or more recycled material films. Using less is not just cheaper; it is also more sustainable and more productive, as you don’t need to worry about a sub-supplier running out of stock quite as often.
How is digitalisation and the use of big data impacting the aftermarket?
I see digital technologies changing the aftermarket in several areas.
First, we see digital twinning enabling program testing before building the machine and enabling test operation for training technicians. This equals better use of resources, less waste and fewer mistakes. It also paves the way to better on-boarding for new colleagues.
Secondly, I see the increased use of virtual reality and mixed reality impacting quite a lot. There are many solutions out there – we use HoloLens from Microsoft – enabling aftermarket services to be more precise and of better quality. For instance, if you need to instruct an operator on the other side of the planet to fix something on a machine or simply feed another sheet into a packing machine, you can now utilise the glasses’ ability to add an extra layer on top of what they can see and give the instructions right where the operator is working.
Thirdly, documentation without paper is very much in demand. And so it should be:We can control documents from a central perspective and ensure all things are kept up-to-date and relevant. This reduces workload and paperwork, and it increases safety and productivity. We want to help our clients access documentation via innovative technologies and user interfaces like QR codes and update it digitally - however, it challenges the individual company’s data policy, as being able to let an ‘outsider’ tamper with data is seen as a safety breach.
How do you solve this in a world where digital attacks and hacking is increasing?
Effective IT security requires a comprehensive approach that involves technical measures, strong policies, and procedures. It’s important to keep updated on security threats and technologies and to have a strategy in place for dealing with any possible security issues.
We continuously exert our best effort to produce long-lasting quality while minimising resource demand, energy use, and maintenance. Data is crucial to us in order to assist our clients in becoming even better. To do this successfully we need data. We must ensure that these systems are secure in order to protect against threats that could jeopardise vital data or disrupt business operations.
Want to know more?
Find more information about what we can offer here