5 key trends in manufacturing automation – and why they matter
In this blog, we examine the five key trends we think will play an important role automation in general in the new year – and especially as concerns automating the manufacture of insulation and large boards. To do so, we’ll look at both the automation trends themselves and at the business drivers underlying the trends.
Trend 1: Optimizing automation performance is more important than ever, so monitoring automation processes and diagnosing problems will be increasingly in focus
As our customers face increased competition – and get by with lower headcount – they are looking for every means possible to boost the efficiency of their manufacturing automation processes and decrease costs. In our experience, all customers define efficiency in their own way but there are some common interests. The focus on equipment performance is one, with “overall equipment efficiency” (OEE) coming up in more and more discussions. The use of data to measure and report on performance is another.
In 2018, we’ll be collecting higher volumes of more kinds of data from automated production lines – and building this data collection into more projects – than ever before. The more data we have, the better analyses we can do regarding optimization.
Collecting the data is one thing. Knowing what to collect is another. Knowing how to analyze and present actionable data for shop floor management and operators comprises yet another essential skillset. We’re building sensors, software systems, and reporting devices that do this in increasingly intelligent ways.
Of course, capacity utilization and the types and number of production errors are still important, but other kinds of data are also making their mark. One key OEE metric is the number of sellable products coming off the finishing end. This can be hard to measure while the line is running but we find that consistently analyzing this metric in a structured way invariably leads to increased performance.
Another critical parameter getting more attention is line speed over time. Although there may be peaks where the line runs even faster than 100%, if the line process is unstable you might end up with an overall line speed at only 80% when measured over a longer period.
Another example of the increased drive for efficiency is the spread of video surveillance of automated production lines. Alongside dynamic performance dashboards, these video feeds are displayed on large screens on the production floor or in remote locations and recorded for later use.
Relatively low-tech and simple to use, video recording of critical spots on automated production lines is nonetheless a powerful diagnostic tool to troubleshoot problem areas and increase efficiency. Managers and operators can review video clips to determine what went wrong – and where and when it happened – adding more eyes without adding more headcount.
Trend 2: Turnkey deliveries are getting more comprehensive and becoming more common
We are increasingly supplying entire turnkey automation systems – not just sections and components. And we expect this trend to accelerate in 2018 and beyond.
One reason for this is that competitive forces are driving customers to apply razor-sharp prioritization between must-have, core competencies and “nice-to-have” capabilities. Fewer and fewer employ their own engineering and automation resources. Increasingly, companies are outsourcing the design, production, and maintenance of automation equipment to specialist partners. Another reason is that is that many customers, not least in Western countries, continue to struggle with a lack of skilled and trained personnel, especially engineering resources, programmers and skilled labor for maintenance.
These complex turnkey systems comprise everything the customer needs to automate a production line, including:
- Hardware
- Software
- User interfaces
- Data analysis
- Installation and training
- Spare parts and maintenance
Trend 3: We’ll see more strategic procurement partnerships
This trend is closely related to the one we describe above and is driven by the same underlying causes: less in-house expertise in none-core capabilities and more strategic outsourcing.
We are working more and more as consultants. Not just supplying hardware, software and all the rest, but cooperating closely with customers to understand their business priorities, competitive situation and strategies – and how their goals can best be met through manufacturing automation.
The closer we get to customers, the better we can serve their needs. We are more and more a trusted partner in this regard – not just a vendor.
Trend 4: User interfaces are getting smarter
In 2018, we expect the trend of increasingly smart interfaces and control panels to manage and optimize automation processes to pick up even more speed.
Don’t even think about complex PLC interfaces. Consider instead the simplicity and versatility of an iPad.
Why? As mentioned above, to deal with the growing skills gap. Companies are having a hard time recruiting and retaining skilled labor for increasingly automated production environments. When the old guys leave, the new guys don’t have the experience or insight to make things work. In lieu of experienced staff and more training, user interfaces must become more intuitive and easy to understand. Customers need interface solutions that capture and transfer collected experience. Operators must be able to quickly and easily do what they need to do. We will see more YouTube-like “how to” videos, “if this happens, then do that” instructions, and better visuals instead of more text.
Trend 5: Expect more flexibility to be built into more automation systems – with the help of more robots
Automation customers are increasingly keen on investing in equipment that can adapt to evolving product innovations, customization requirements, and process improvements.
Time to market is important, as is changeover speed. Capital investments are under a lot of scrutiny, and managers want to be sure they can change and scale new equipment without replacing it. While they know that “future-proof” is impossible, they are asking us to build in more flexibility than ever before.
Flexibility is engineered in many ways, but robots play an important role. As the commoditization of robots continues, robotic solutions become better, more flexible and cheaper. We will see more and more focus on using industrial robots to either replace or supplement specially designed equipment in 2018.
At Qubiqa we try to combine the best from two worlds: specially designed equipment and industrial robots.
Contact me
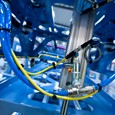